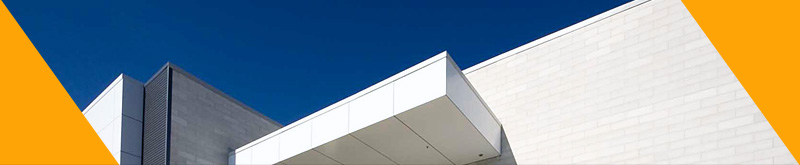
FAQ
- About the BenexBlock™
- Working with the BenexBlock™
- Purchasing BenexBlock™
- Technical questions
- Installation of BenexBlock™
- BenexMix Adhesive
- Render
- Environmental
- Material Data Safety Sheets (MSDS)
- Other
The Benex Masonry embodied energy is determined in the following way: Density 1,000kg/m³.
Constituent | % by weight | Embodied Energy MJ/kg |
Off-white cement | 34.2% | 1.92 |
Fine sand | 46.1% | 0.37 |
Polystyrene beads (2-3 mm) | 1.3% | 1.57 |
Water | 18.3% | 0.00 |
Other processes | 0% | 0.15 |
Calculated Total | 100.0% | 4.00 |
Not at this stage, but large orders would be considered.
If the polystyrene beads are visable through the product is this an issue?
Not at all. This is a natural part of the process and goes to the honesty of our product.
The most common method of cutting Benex™ is with a Wet-saw. It's best to use 210mm-220mm so you do not need to rotate the block when cutting. Tungsten Carbide Tipped hand saws can also be used. If using a dry saw, there may be dust generated and the appropriate precautions should be considered.
All of the CSIRO tests were carried out on non-core filled walls and blocks. Benex™ offers a four hour loading bearing fire rating without any core-fill material, however, the need for core-filling will be determined by your project engineer and the specific application.
Benex™ as a stand alone product is impervious to water, as is the BenexMix adhesive. The base course of a Benex Wall requires traditional brickies mortar which needs additional additives for waterproofing. The most susceptible area for water to penetrate any constructed block wall is within its joints. Therefore, it is imperative that the Benex Block Installer runs two continuous beads of glue (8-10mm thick) on both the length of the block on both sides and vertically on both sides of the blocks to ensure water cannot penetrate the block at the joints. If the Benex Installer hasn't sealed every course adequately there may be a possibility for water to penetrate and for this reason BenexBlock™ cannot offer a 100 % guarantee.
This will depend on the applied loads and the application. Please discuss specifics with your Benex™ representative.
No, but Benex dry out very quickly unlike traditional concrete blocks and can be installed virtually as soon as the rain stops.
Simply notch the blocks with a scutch hammer or similar and install the reinforcement in accordance with your engineers details. The workability and texture of the BenexBlock™ ensures this can be completed much more efficiently than traditional blocks. Benex are planning to install the required equipment into our next generation plants to produce a specific block for horizontal reinforcement.
If installed correctly, no, however, for areas that must be remain absolutely dry, it may be worthwhile applying auxiliary support such as a waterproof membrane.
A safe approach is to work to the BCA (Building Code of Australia) which limits control joints to 6m. However as the Benex Blocks are very stable and generally shrink less than most other cement based masonry products a safe limit is 8m.
You should always consult your structural engineer to ensure control joints are located correctly.
Yes, one of the unique properties of Benex is that they can be drilled and cut to almost any shape without cracking.
Mix the BenexMix Adhesive into a thicker consistency and apply using a broad knife or similar. Once the BenexMix in the damaged area starts to dry, sponge the area and the adhesive will cure to a colour that is similar to the block. It may be necessary to reapply for larger damaged areas.
This entirely depends on the application. Retaining walls may need to be core filled at a very low height, whereas other walls may be built up to 6m without core filling or reinforcement.
Currently, Benexk™ is available direct to the public. Please contact us for more information.
Please contact us for pricing information. You may also refer to the Comparison Chart located within Technical Data.
Please contact us for pricing information.
Please refer to the Comparison Chart page located under Technical Data.
R = 0.52 (as untreated wall).
R = 2.5 (as a composite wall without render or paint) – see additional info about Air-Cell and composite walls in the Thermal Properties document under Technical Data.
Note: Some high performance acrylic renders and paints can provide significant thermal performance when applied to a Benex wall. However, this generally only applies to those areas directly exposed to sunlight.
RW37 – based on Benex™ as a standalone product.
RW50 – as a core-filled Benex™ wall.
RWSTC52 – by adding 25mm batten either steel or timber with a rubber blanket followed by 10mm of plasterboard.
Within Australia, the Australian Standard, AS3700 Masonry Structures provides guidelines to design a Benex™ building. Additional information can be found with the Technical Data section of this website. The Benex block wall replaces most masonry products and wall systems. The overall thickness of a Benex Wall is 200mm. The Benex Composite Wall System is 250mm thick overall (which replaces traditional Brick Veneer and Double Brick walls).
The H600R Benex Block is 7.07mpa and the S600R Benex Block is 15.68mpa. For more information, please refer to Page 18 of the Structural Properties document in Technical Data.
The Benex Technical Manual can be down loaded directly from this website. This is located under our Technical Data section.
Refer to the Technical Data section of this website
Subject to availability, a Benex Installer may be able to train site staff and address any questions specific to the project. Typically this will be for orders exceeding 200m².
Benex can provide a Technical Officer on site, for projects that require over 200m² of product, to establish the works and conduct initial training as required. This service will ensure that our product is installed as per our specifications. If you require the service of a Technical Officer on site then please inform your Benex Sales Representative when you submit your order. If Benex provide assistance for a project, there may be some costs. This will be determined at the time of quoting the project.
Benex can nominate a list of installers. It will then be the responsibility of the client to chose the most appropriate installer as Benex cannot control the workmanship of every project involving these installers.
No, BenexMix Adhesive must be used on all courses excluding the first course.
Benex Glue Guns were used for all the CSIRO tests and should be used to install Benex Blocks. Benex Glue Guns ensure there are two continuous beads of glue (8-10mm thick) on both the length of the block on both sides and vertically on both sides of the blocks which ensure water cannot penetrate the joints. Secondly, using the Benex Glue Guns minimizes wastage and leaves less mess on site. The use of Brickie Trowels is not recommended.
From 6 – 10m² depending on usage and wastage.
No, as the Benex wall provides an aesthetic face finish. Personal preference will influence how the client chooses to complete the finished wall.
Both sides of the Benex Blocks can be rendered.
Traditional cement render adheres well to the rough side of the Benex Blocks without any additional preparation, but will need to be prepared if applied to the smooth face.
Acrylic renders will adhere to either side of the Benex Blocks without any special treatment or preparation and can offer substantial thermal benefits over traditional cement renders. Contact Benex for the most suitable render for your project.
Either Acrylic or Cement based renders can be used. If using cement based render please follow the recommended mix for traditional cement. Refer to the Cement Render page in the Technical Data section.
Comparing Benex™ to traditional masonry products: Sometimes less is more!
- Less energy used in manufacturing.
- Less energy used in delivery.
- Less water usage during manufacture.
- Less energy used over the life of building.
- Less weight per m² (up to 60% less).
The Benex manufacturing method is unique and uses a lot less energy than traditional masonry products. As an example, at Benex we use the waste heat from the compressor that runs the Benex plant to heat the drying chamber. Virtually no other energy is used to dry the Benex Blocks.
Benex is up to 60% lighter per m² of wall than most other masonry products. This means much less fuel is used to get the Benex products to the building site. A single delivery of Benex to a building site can have over 300m² of Benex Blocks, this includes the BenexMix Adhesive, so you will not require the usual additional deliveries of sand and cement (apart from the first course).
Also, a typical Benex wall will only require a fraction of the water that would be used in a traditional masonry wall.
It is worth noting that a Benex wall is thermally superior to almost every other masonry product. This means less energy will be used to heat and cool a Benex Building.
In summing up, less energy to make and deliver the Benex Blocks and almost no water in comparison to traditional masonry products and less energy will be used over the life of the building when built out of Benex Blocks.
We harvest our own rainwater and use this as much as possible.
We have started trials on cement replacement products that are completely recycled and will reduce our usage of cement by more than 35%. We are also looking at alternatives to mined sand and will be starting trials on this technology as soon as practical. There are also a number of alternatives to polystyrene that will be thoroughly investigated over in the near future.
As is the case with all cementitious products, installers should exercise caution and take the appropriate safety measures to eliminate risk. Please refer to the Material Safety Data Sheets (MSDS) located within the Technical Data section of this website.
Refer to the Technical Data section of this website.
Not currently but watch this space.
Please contact us.